Destylarka do rozpuszczalników
Destylarka do rozpuszczalników to urządzenie, które wykorzystuje proces destylacji do oddzielania różnych substancji na podstawie ich temperatury wrzenia. Proces ten jest niezwykle istotny w wielu branżach, takich jak przemysł chemiczny, farmaceutyczny czy kosmetyczny. W destylacji wykorzystywane są różne rodzaje destylarek, w tym te o dużej wydajności, które mogą przetwarzać znaczne ilości cieczy. W przypadku rozpuszczalników, destylacja pozwala na odzyskiwanie cennych substancji chemicznych, co nie tylko zmniejsza koszty produkcji, ale również przyczynia się do ochrony środowiska poprzez ograniczenie odpadów. W praktyce, destylarka składa się z kilku kluczowych elementów, takich jak zbiornik na ciecz, kolumna destylacyjna oraz kondensator. Każdy z tych komponentów odgrywa istotną rolę w procesie oddzielania składników.
Jakie są najpopularniejsze rodzaje destylarek do rozpuszczalników
Na rynku dostępnych jest wiele różnych typów destylarek do rozpuszczalników, które różnią się zarówno budową, jak i przeznaczeniem. Najpopularniejsze z nich to destylarki prostokątne oraz cylindryczne. Destylarki prostokątne charakteryzują się większą powierzchnią wymiany ciepła, co pozwala na szybsze i bardziej efektywne oddzielanie składników. Z kolei destylarki cylindryczne są bardziej kompaktowe i często stosowane w mniejszych laboratoriach lub zakładach produkcyjnych. Innym popularnym rozwiązaniem są destylarki rotacyjne, które umożliwiają delikatną destylację w niskich temperaturach, co jest szczególnie ważne dla substancji wrażliwych na wysoką temperaturę. Warto również wspomnieć o destylarkach próżniowych, które działają w obniżonym ciśnieniu, co pozwala na obniżenie temperatury wrzenia substancji i minimalizację ryzyka ich degradacji.
Jakie są zalety korzystania z destylarki do rozpuszczalników
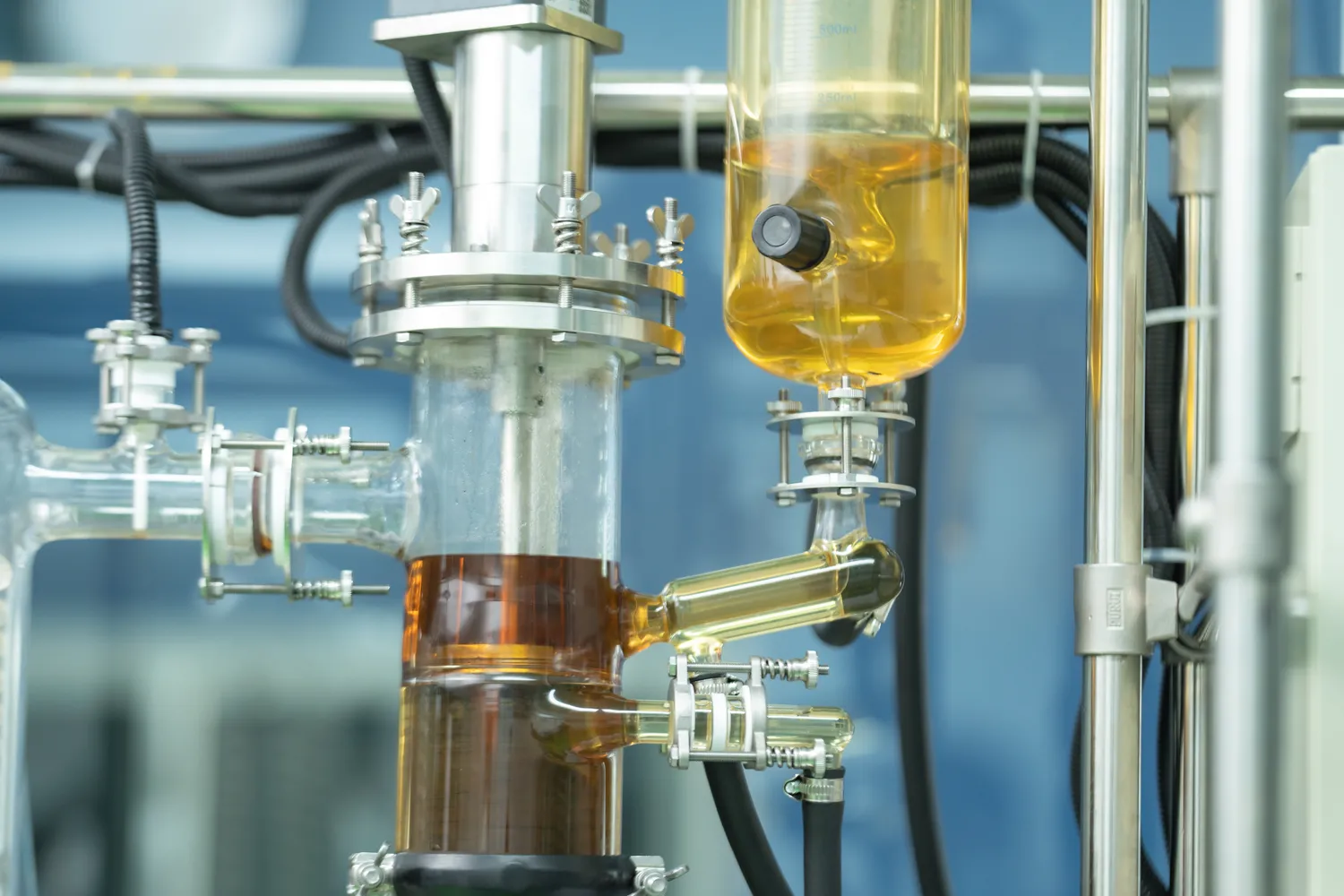
Korzystanie z destylarki do rozpuszczalników niesie ze sobą wiele korzyści zarówno dla producentów, jak i dla środowiska. Przede wszystkim umożliwia ona skuteczne odzyskiwanie cennych substancji chemicznych, co przekłada się na oszczędności finansowe. Dzięki temu procesowi możliwe jest ponowne wykorzystanie rozpuszczalników w produkcji, co zmniejsza zapotrzebowanie na nowe surowce oraz ogranicza generowanie odpadów. Dodatkowo, nowoczesne destylarki są projektowane z myślą o efektywności energetycznej, co oznacza mniejsze zużycie energii podczas procesu destylacji. Kolejną zaletą jest możliwość uzyskania wysokiej czystości produktów końcowych, co jest kluczowe w branżach wymagających ścisłych norm jakościowych. Użycie destylarek przyczynia się także do poprawy bezpieczeństwa pracy w zakładach przemysłowych poprzez minimalizację ryzyka związane z przechowywaniem i używaniem dużych ilości chemikaliów.
Jakie czynniki wpływają na wybór odpowiedniej destylarki do rozpuszczalników
Wybór odpowiedniej destylarki do rozpuszczalników powinien być dokładnie przemyślany i oparty na kilku kluczowych czynnikach. Przede wszystkim należy zwrócić uwagę na rodzaj przetwarzanych substancji oraz ich właściwości fizykochemiczne. Różne rodzaje rozpuszczalników mają różne temperatury wrzenia oraz wymagania dotyczące warunków pracy, dlatego tak ważne jest dopasowanie sprzętu do specyfiki procesu. Kolejnym istotnym czynnikiem jest wydajność urządzenia – im większa wydajność, tym szybciej można przetwarzać surowce i uzyskiwać gotowe produkty. Należy również uwzględnić aspekty związane z kosztami eksploatacyjnymi oraz konserwacją urządzenia. Warto zwrócić uwagę na nowoczesne technologie, które mogą zwiększyć efektywność procesu oraz zmniejszyć zużycie energii.
Jakie są najczęstsze problemy związane z użytkowaniem destylarki do rozpuszczalników
Użytkowanie destylarki do rozpuszczalników, mimo wielu zalet, może wiązać się z różnymi problemami, które mogą wpływać na efektywność procesu oraz bezpieczeństwo pracy. Jednym z najczęściej występujących problemów jest niewłaściwe ustawienie temperatury, co może prowadzić do nieefektywnej destylacji lub nawet degradacji przetwarzanych substancji. W przypadku zbyt wysokiej temperatury istnieje ryzyko, że delikatne składniki chemiczne ulegną zniszczeniu, co negatywnie wpłynie na jakość końcowego produktu. Innym problemem mogą być zatory w kolumnie destylacyjnej, które mogą powstać w wyniku osadzania się substancji na ściankach kolumny. Zatory te mogą ograniczać przepływ pary i prowadzić do obniżenia wydajności urządzenia. Dodatkowo, niewłaściwe uszczelnienia mogą prowadzić do wycieków substancji chemicznych, co stanowi zagrożenie dla zdrowia pracowników oraz środowiska.
Jakie są najlepsze praktyki dotyczące obsługi destylarki do rozpuszczalników
Aby maksymalizować efektywność i bezpieczeństwo użytkowania destylarki do rozpuszczalników, warto przestrzegać kilku najlepszych praktyk. Przede wszystkim kluczowe jest dokładne zapoznanie się z instrukcją obsługi dostarczoną przez producenta. Znajomość specyfikacji technicznych oraz zasad działania urządzenia pozwala uniknąć wielu problemów związanych z jego eksploatacją. Ważne jest również regularne przeprowadzanie konserwacji oraz czyszczenia wszystkich elementów destylarki, aby zapewnić ich prawidłowe działanie. Należy także monitorować parametry pracy urządzenia, takie jak temperatura czy ciśnienie, aby szybko reagować na ewentualne nieprawidłowości. Kolejną istotną kwestią jest zapewnienie odpowiedniej wentylacji w pomieszczeniu, w którym znajduje się destylarka, aby zminimalizować ryzyko gromadzenia się oparów chemicznych.
Jakie są koszty zakupu i eksploatacji destylarki do rozpuszczalników
Koszty zakupu i eksploatacji destylarki do rozpuszczalników mogą się znacznie różnić w zależności od wielu czynników, takich jak typ urządzenia, jego wydajność oraz dodatkowe funkcje. Na rynku dostępne są zarówno proste modele przeznaczone dla małych laboratoriów, jak i zaawansowane systemy przemysłowe o dużej wydajności. Koszt zakupu prostszej destylarki może wynosić kilka tysięcy złotych, podczas gdy bardziej skomplikowane systemy mogą kosztować dziesiątki tysięcy złotych. Oprócz kosztów zakupu należy również uwzględnić wydatki związane z eksploatacją urządzenia, takie jak zużycie energii elektrycznej, koszty materiałów eksploatacyjnych oraz konserwacji. Regularne przeglądy techniczne oraz serwisowanie sprzętu również generują dodatkowe koszty. Warto jednak zauważyć, że inwestycja w nowoczesną destylarkę może przynieść znaczne oszczędności w dłuższej perspektywie dzięki efektywnemu odzyskiwaniu rozpuszczalników i zmniejszeniu kosztów surowców.
Jakie innowacje technologiczne wpływają na rozwój destylarek do rozpuszczalników
Rozwój technologii ma ogromny wpływ na ewolucję destylarek do rozpuszczalników, co przekłada się na ich wydajność oraz bezpieczeństwo użytkowania. W ostatnich latach pojawiły się liczne innowacje mające na celu poprawę efektywności procesów destylacyjnych. Jednym z najważniejszych trendów jest zastosowanie automatyzacji i inteligentnych systemów zarządzania procesami produkcyjnymi. Dzięki nowoczesnym czujnikom i oprogramowaniu możliwe jest monitorowanie parametrów pracy w czasie rzeczywistym oraz automatyczne dostosowywanie ustawień urządzenia do zmieniających się warunków. Innowacyjne materiały używane do budowy destylarek również przyczyniają się do poprawy ich wydajności – nowe kompozyty czy powłoki antyadhezyjne zmniejszają osadzanie się substancji na ściankach kolumny destylacyjnej. Ponadto rozwijają się technologie związane z odzyskiwaniem energii, co pozwala na zmniejszenie kosztów eksploatacyjnych i ograniczenie wpływu na środowisko naturalne.
Jakie regulacje prawne dotyczą użytkowania destylarek do rozpuszczalników
Korzystanie z destylarek do rozpuszczalników podlega różnym regulacjom prawnym mającym na celu ochronę zdrowia ludzi oraz środowiska naturalnego. W wielu krajach istnieją przepisy dotyczące przechowywania i transportu substancji chemicznych, które muszą być przestrzegane przez przedsiębiorstwa zajmujące się ich przetwarzaniem. W Unii Europejskiej kluczowym dokumentem regulującym kwestie związane z substancjami chemicznymi jest Rozporządzenie REACH (Registration, Evaluation, Authorisation and Restriction of Chemicals), które nakłada obowiązki rejestracyjne na producentów i importerów substancji chemicznych. Ponadto przedsiębiorstwa muszą stosować się do przepisów dotyczących ochrony środowiska oraz zasad BHP w miejscu pracy. W przypadku użytkowania destylarek ważne jest także przestrzeganie norm emisji gazów oraz odpadów chemicznych wynikających z procesu produkcji.
Jakie są przyszłe kierunki rozwoju technologii destylacji
Przyszłość technologii destylacji zapowiada się obiecująco dzięki ciągłemu postępowi naukowemu oraz innowacjom technologicznym. W miarę rosnącej świadomości ekologicznej społeczeństwa coraz większy nacisk kładzie się na rozwój procesów przyjaznych dla środowiska. Oczekuje się wzrostu zainteresowania technologiami umożliwiającymi odzyskiwanie energii oraz zmniejszenie zużycia surowców naturalnych podczas procesów produkcyjnych. Również rozwój nanotechnologii może przyczynić się do poprawy efektywności procesów destylacyjnych poprzez zastosowanie nowych materiałów o lepszych właściwościach termicznych i chemicznych. W przyszłości możemy również spodziewać się większej integracji systemów informatycznych z procesami przemysłowymi – inteligentne algorytmy będą mogły optymalizować parametry pracy urządzeń w czasie rzeczywistym, co zwiększy ich wydajność i bezpieczeństwo użytkowania.